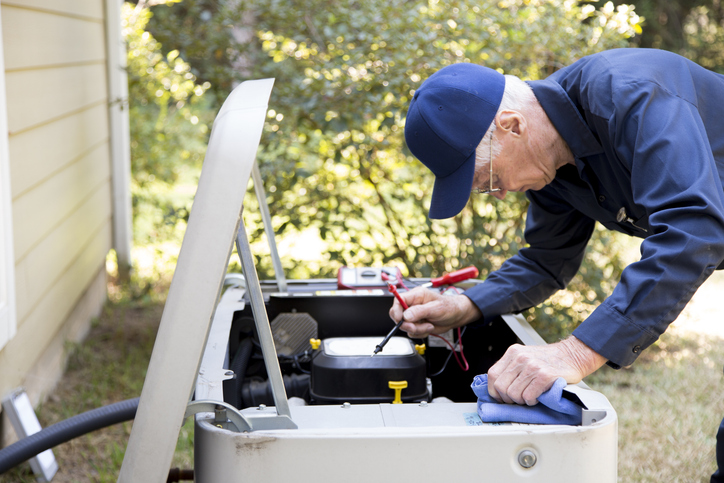
Innovations in Generator Maintenance: Remote Solutions
Generator maintenance has transformed significantly through technological progress. Smart solutions now make equipment care easier and more efficient. Innovations in generator maintenance continue to reshape how we handle power backup systems. These advances help businesses prevent breakdowns and extend equipment life.
Remote monitoring represents a significant breakthrough in generator upkeep. Sensors and software now track performance data in real time. Technicians can spot issues before they become serious problems. This proactive approach has revolutionized how companies maintain their power systems.
These systems offer several key benefits:
- Early problem detection helps prevent unexpected breakdowns and reduces repair costs significantly
- Real-time data analysis enables maintenance scheduling based on actual usage patterns and performance metrics
- Remote access allows technicians to monitor multiple generators from a central location, improving efficiency
- Automated alerts notify maintenance teams when parameters fall outside normal ranges
Data-Driven Maintenance Solutions
Predictive analytics has revolutionized how we approach innovations in generator maintenance. This technology uses historical data to forecast potential equipment issues. By analyzing patterns and trends, companies can prevent problems before they occur.
The system analyzes various factors like:
- Runtime hours and load levels across different operating conditions
- Environmental conditions affecting performance and efficiency levels
- Component wear patterns and expected lifetime calculations
- Maintenance history and repair records for similar equipment models
- Performance benchmarks against industry standards
Innovations in Generator Maintenance: Advanced Testing Technologies
Modern testing methods have improved maintenance precision. Ultrasound testing detects internal component issues without invasive procedures. Thermal imaging identifies hidden hotspots through infrared technology. These advanced methods provide deeper insights into equipment health.
Companies now use sophisticated testing equipment to:
- Measure electrical connections and component integrity
- Monitor bearing conditions and lubrication levels
- Track fuel quality and consumption patterns
- Assess cooling system efficiency
Smart Maintenance Solutions
Condition-based maintenance represents a shift from traditional scheduling. Instead of fixed intervals, maintenance occurs when equipment actually needs attention. This approach saves time and reduces unnecessary servicing. It also helps companies optimize their maintenance budgets.
Digital twin technology creates virtual models of physical generators. These simulations help technicians:
- Test different maintenance scenarios without risking equipment damage
- Predict equipment behavior under various operating conditions
- Plan upgrades more effectively based on performance data
- Reduce maintenance risks through virtual testing
- Optimize maintenance schedules based on actual usage patterns
Augmented Reality and Cloud Solutions in Generator Maintenance
AR technology enhances maintenance procedures through digital overlays. Technicians access essential information while working on equipment. This innovation reduces errors and improves repair efficiency. Step-by-step guidance ensures consistent maintenance quality.
Cloud-based systems store vast amounts of maintenance data. This centralized approach helps companies:
- Track generator performance across multiple locations in real-time
- Access maintenance history instantly for better decision-making
- Share information between team members seamlessly
- Make data-driven decisions about equipment care and upgrades
- Generate comprehensive maintenance reports automatically
The Future of Power System Maintenance
The landscape of generator maintenance continues to evolve. New technologies emerge regularly, offering improved ways to maintain power systems. Companies that adopt these innovations gain significant advantages in reliability and efficiency.
Future developments may include:
- Artificial intelligence systems for automated maintenance scheduling
- Advanced sensor technologies for more precise monitoring
- Improved battery storage solutions for backup power
- Enhanced integration with smart building systems
- More sophisticated predictive maintenance algorithms
Integration and Implementation
Successful implementation of these maintenance innovations requires proper planning. Companies should:
- Assess their current maintenance practices and identify areas for improvement
- Train maintenance staff on new technologies and procedures
- Develop clear protocols for using advanced maintenance tools
- Monitor and evaluate the effectiveness of new maintenance approaches
- Adjust strategies based on performance data and results
Contact Oasis AC Services at (225) 414-0708 for expert generator maintenance using the latest technological innovations. Their team ensures your power systems run smoothly with cutting-edge maintenance solutions and professional expertise.